the future of load restraint
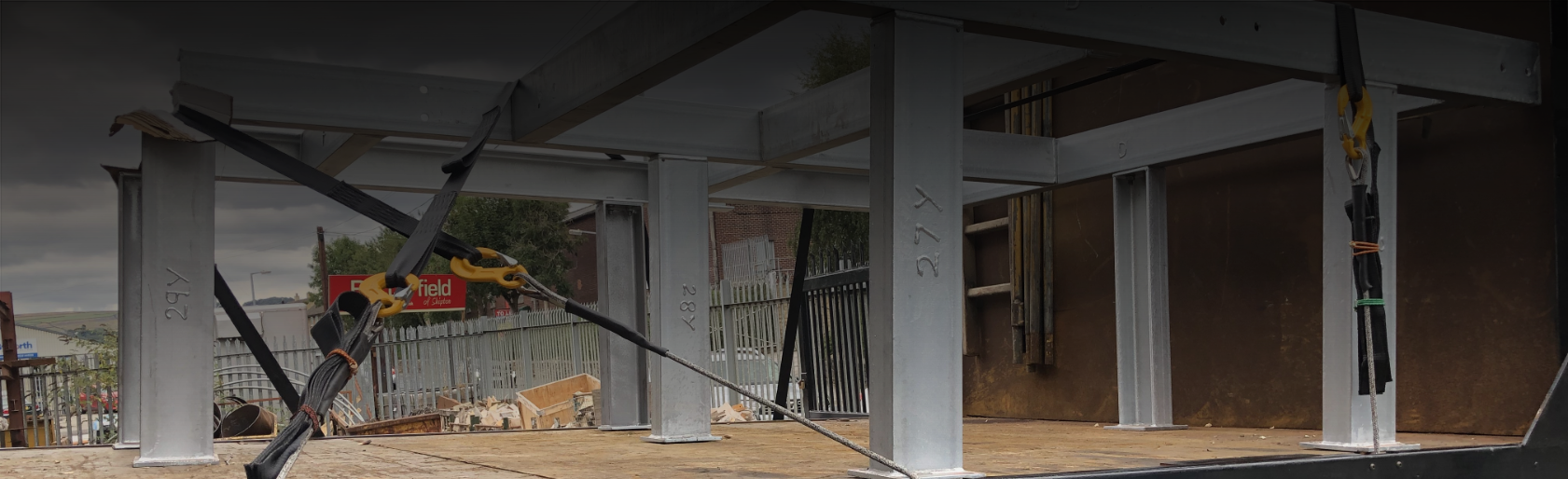
Conventional Ratchet Straps –
Associated Challenges
Conventional lever 50kg needed to exact 350kg in line (Rated STF – standard tensioning force)
This 50kg figure is twice the accepted figure in the manual handling guidelines
The driver has no way of measuring the applied load
For same applied force a handle line tension reduces with age
Tension release is difficult to action & this only gets worse with age
The strap can lock up if the strap fouls in the mechanism
Ironic that lifting gear is subject to mandatory testing and inspection whereas no guidelines for strapping down truck loads
Cost of replacing lost and worn parts equate to £300 / truck/trailer per year
Benefits
of Auto Tensioner System
For every lashing point on the typical truck/trailer our auto tensioner provides a one-minute saving
Guaranteed and consistent lashing force applied
Effortless application and release
Complies with DVSA guidelines
Defends operator’s licence (PG9’s)
Reduces goods in transit damage / claims
Employers and Public liability insurance – potential for reduction
Reduced operator fatigue / RSI

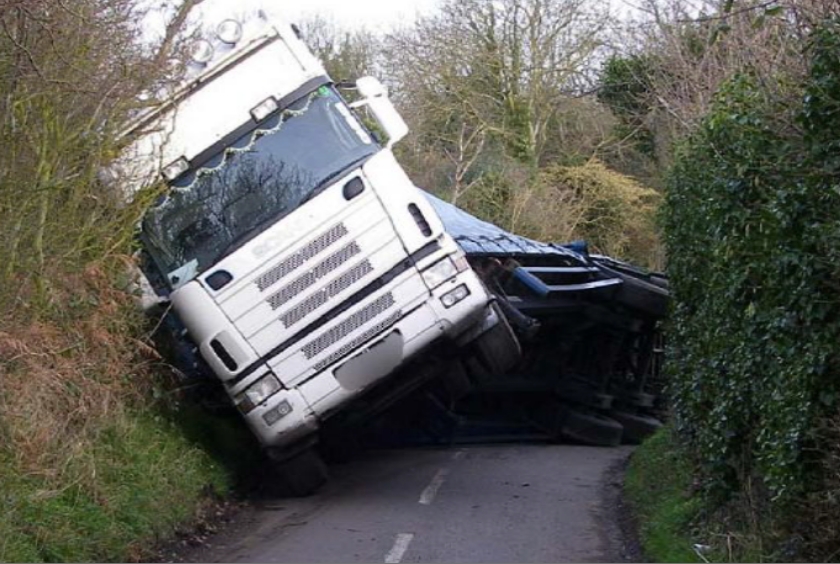
CHALLENGES
There are many publications highlighting the problems associated with load restraint, some of which can be accessed through this website (please see the legislation guidance).
One of the main underlying causes is the time and effort required by the driver to secure the load. The pressure to get mobile may influence the driver to make poor decisions about load control.
Our auto-tensioners are rapid (2/3 seconds) and require minimum effort to operate the valve lever. This makes the securing operation much less daunting for the driver and he’ll be on the road again much sooner knowing that his load is safe.
Solutions
In making the securing operation more efficient, the likelihood of prosecution is greatly reduced as is the chance of load slip and potential injury to the driver and other road users. The special rope used in our tensioners has a breaking strength of 9 tonnes and the units are rated at LC2000daN. They have been designed to meet the requirements of BS EN 12195-2 and the lashing points requirements of BS EN 12640.
After tensioning, each unit is locked out during transit and remains that way until the driver wishes to release them. As such they are tamper proof and cannot be released until the driver is ready.
They’ve been designed to last the lifetime of a typical trailer with no maintenance.
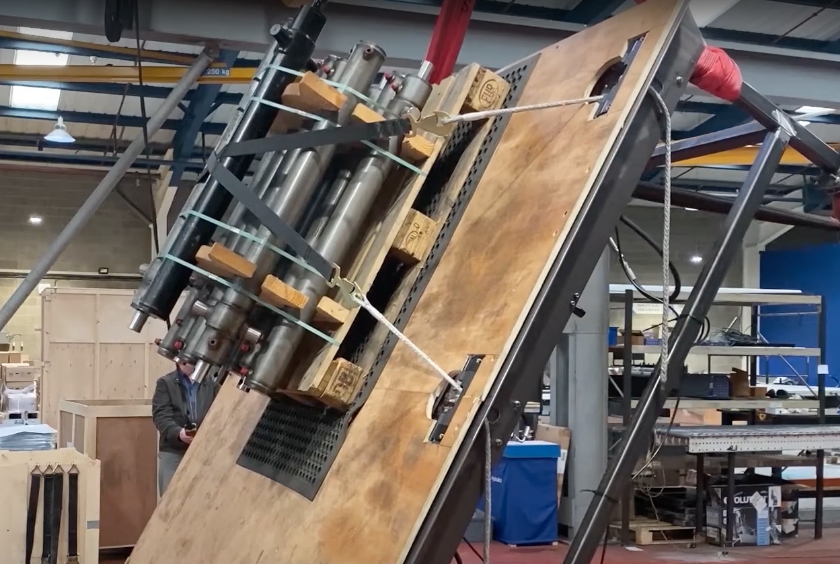
FAQ Questions...
Got a question ? Maybe these will help, if not drop us a line on our contact page.
call 01535 288612 for a free demonstration with our fully equipped vehicle
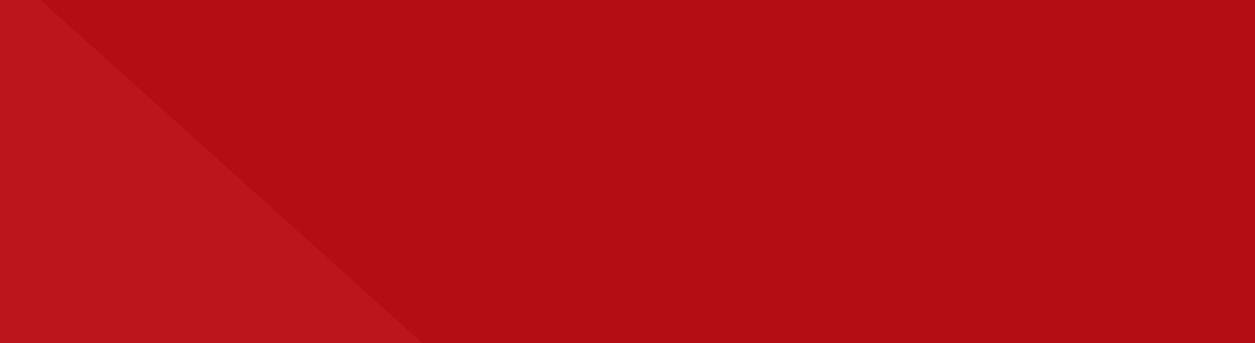